
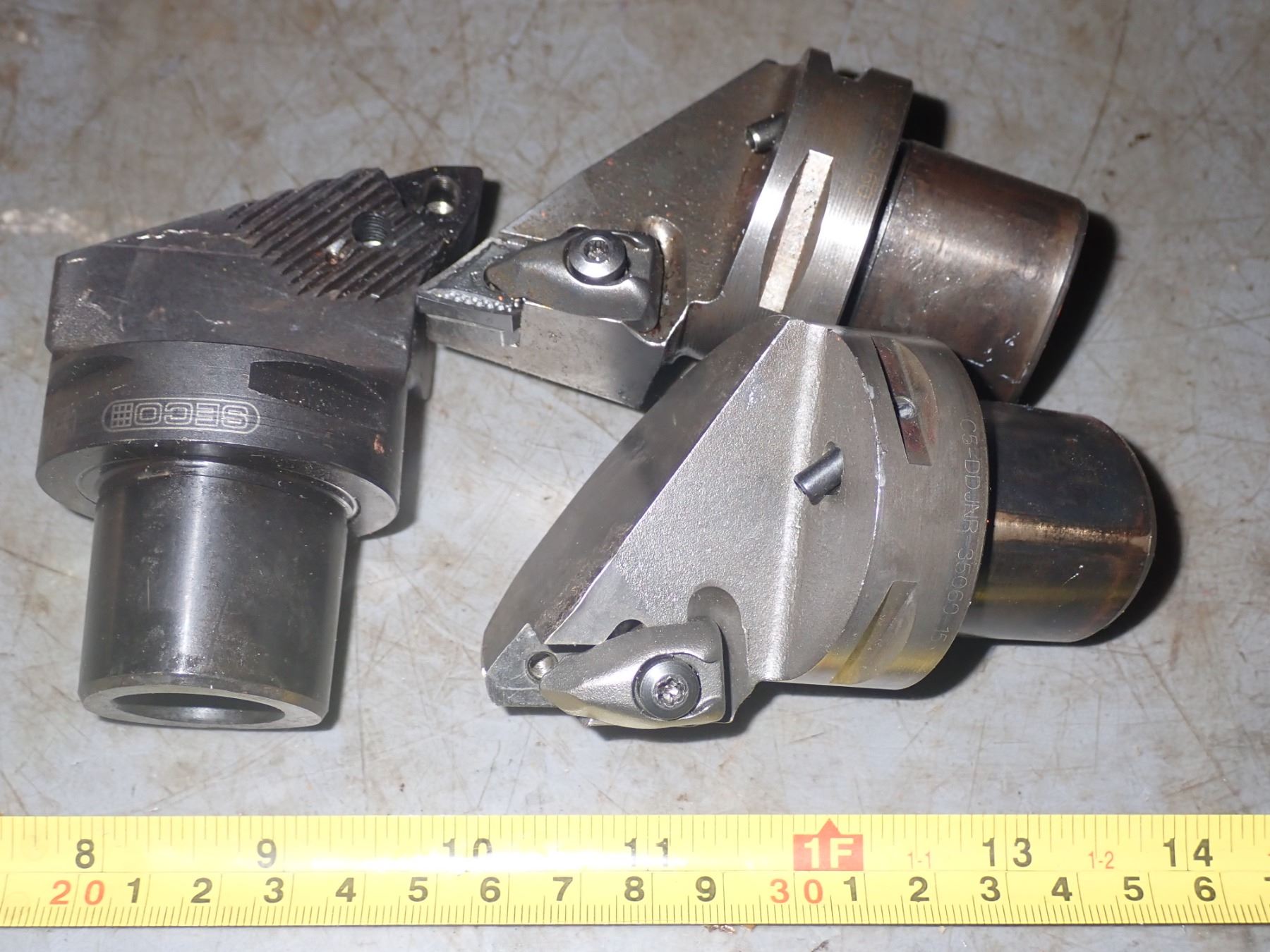
The vibration dampening system is preset at the factory, eliminating the need for fine-tuning of the dampening function prior to use, the company says. Unlike conventional steel or solid carbide boring bars that are often ineffective at length/diameter ratios beyond 6xDc, Walter’s Accure∙tec A3001, with its patented vibration dampening system, is said to excel at length/diameter ratios beyond 6xD up to 10xD. With the A3001 and the A2201, Walter has increased boring bar diameters to 2.5-4" and 60-100 mm.

The standard A2201 is an offset adaptor for reduced radial forces, greater stability and provides more space between the boring bar and the bore wall for improved chip removal with very deep bores. We should have used KM63.Walter USA has expanded its Accure∙tec anti-vibration boring bar line with the addition of the A3001 boring bar in combination with A2201 intermediate offset adaptor for larger diameter bores. It provides for fast, productive counterboring and internal profiling of parts in industries such as aerospace, oil and gas and general metalworking. Capto or KM will be ok if you choose a size larger than the largest boring bar you use. Changing diameter is very little faster since you must back the masters out before shifting position.Ĭapto might be a better choice if *** the tools are available. We have a Forkhardt quick change chuck and find it to be slower to work with in some cases because we have not bought extra master jaws (very expensive). We end up with about 10 sets of chuck jaws per machine. Loosening 2 bolt and switching jaws is only a few minutes slower than the fastest quick change chuck and the jaws are less expensive. All jaws were sets for specific part diameter, and several had steps of a standard depth (1/4”). We had several sets of nuts for chuck jaws so the operator could be preparing for the next part number to be machined. We had a Wasino LJ63M mill turn for several years and used KM50 and Komet ABS drills to reduce setup time. Capto tooling systems Mechineer (Mechanical) Even though quick change tooling can save some in setup time, the lack of rigidity can increase machining times, scrap, and tool wear to the point of costing more than changing stick tools. With that said, we use Komet ABS drills, some KM tooling and would consider Capto for some jobs. The KM50 was the least stiff and had the greatest non linear deflection. The Capto 50 did not have any low load problems but the deflection became greater as the load increased in a non linear way. of tool pressure in the X direction.Įach of the quick change tools had problems, the ABS 50 was the next most linear in deflection after an initial preload was applied, we saw ±.0005” movement with less than 50 lbs load applied initially.

The most rigid tool was the 1 ½” boring bar, its deflection was linear, for each 10 lbs of load applied the deflection measurement was the same. 0001” indicator was mounted on the turret disk near the tool block and located a specific distance from the load cell point to measure deflection at given loads. The load cell was located the same distance from the joint face on the quick change tools, and from the sleeve on the stick tool. A 2 ½” diameter part was chucked with 4” of stick out, a load cell was connected to the chucked part and the boring bars. The test was done in a new Hitachi HT40G turning center. Tested were new KM 50, Capto 50, ABS 50 boring bars and clamping units, and a 1 ½” steel shank boring bar. Back in 1996 we did stiffness tests with quick change tool joints compared to a 1 ½” boring bar.
